eXquisite detail - it's about what you don't see
by Mark Jardine 15 Aug 19:00 HKT
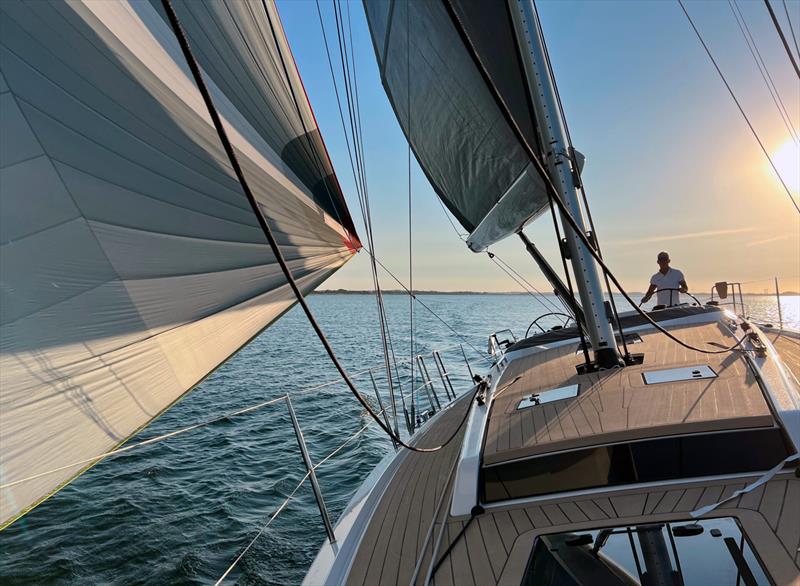
The pure thrill and enjoyment of sailing on an X4.3 © X-Yachts
True quality comes from within. Beneath the beautiful veneers, the flowing lines, the glossy gelcoat and the gleaming brightwork is the precision engineering and craftsmanship which separates the outstanding from the regular.
Visiting the X-Yachts headquarters in Haderslev, Denmark, shows master craftsmen at work, taking pride in what they create, striving to produce a masterpiece every time.
Touring the yard shows how processes are achieved, and the skill that is required to create an X-Yacht. These details, which are often completely hidden from view, explain the strength, longevity and sheer quality of each and every yacht that departs from Haderslev for adventures on the water around the world.
The Hull and Deck
Both the hull and deck are manufactured at X-Yachts' facility in Poland and then transported to Denmark for finishing. They remain in the mould until they have hardened, resulting in an accurate and super-stiff hull. This is one of the reasons that the tolerances when pairing the hull and deck are so fine. The advantage of this is far less filler, and the superior strength gained from a tight bond.
After the hull has been checked for even the slightest air bubble, it is then finished with gelcoat, four layers of primer, then the antifoul.
Seeing the deck fit-out taking place before bonding is always a wonder, with the entire structure supported by only two trollies. This is then laser measured before pairing with the hull to achieve the ultimate accuracy.
A look underneath the deck before hull bonding shows you the strengthening details, such as the carbon reinforcing of the jib track. Something that will be completely hidden once the interior finish is attached.
Seeing a hull in the paint room is a strange experience, as it is hanging from the single point lift attached to the steel frame. We're used to seeing this with sportsboats, but when it's a 50 footer this feels a bit surreal. For the paint room team it means their access is unobstructed, where usually the hull would be sitting in a frame.
Down the companionway
The floorboards, which are backed with rubber for noise dampening, each have screw inserts so that the screws can't damage the wood when attached and removed.
Below decks the diesel tank is aluminium, and the water tank is steel, hung from the steel frame so there is a gap between the hull and the tanks.
The cable runs are also attached to the frame using basket conduits, keeping them tidy, accessible, and out of the bilges.
Take a look in the aft cabins, beneath the companionway and cockpit, and you'll find large access points for the engine, generator, and other utilities, all insulated and finished to a high standard.
Watching a starboard aft cabin cupboard being lowered into the hull with a travel hoist, you can see the craftsmen measure it up, then lightly sand it to make it an exact fit. Instead of having to use excess bonding for the furniture, X-Yachts ensure the fit is right every time.
There is no getting away from the fact that a modern yacht is complex, and the wiring loom is huge. Every wire in an X-Yacht is numbered at each end and catalogued, so owners know exactly what each wire does. When it comes to diagnostics and maintenance, this kind of detail becomes essential, and makes any repairs or replacements far easier.
Below the surface
The keel of an X-Yacht is made in a mould, sheathed in glass, then faired. When sheathing the steel and lead keel in fibreglass, nylon washers are added either side so that when the keel is in the final mould, it sits perfectly central. This is then epoxy infused, and put in the oven to cure.
Even though the keels come out of the mould symmetrical, they are then hand-finished to give a perfectly smooth finish. Combined with the new-shape rudder, this means the underwater surfaces are optimal.
The process very much reminds me of a documentary I watched about Aston Martin when making a car, using craftsmen to ensure the final finish is perfect.
When the keel is bonded to the hull and bolted to the galvanised steel frame, it helps explain why, in over 45 years and with 6,000 yachts built, an X-Yacht has never lost a keel.
The end product
It almost seems a shame that so much of the magic which makes an X-Yacht unique is hidden away, but at the end of the day, it is the engineering which makes the beautiful possible. It is the reassurance of reliability, the solace of safety, the certainty of comfort.
The detail is eXquisite, even if you can't see all of it.
Find out more at www.x-yachts.com
For more details contact Kevin Wallis – Australia & New Zealand Managing Director ( M ) +61 414 258666 or ( E )
For more details contact Kevin Wallis – Australia & New Zealand Managing Director ( M ) +61 414 258666 or ( E )